PEIpro® is the leading PEI-based DNA transfection reagent that offers flexibility and scalability for viral vector manufacturing.
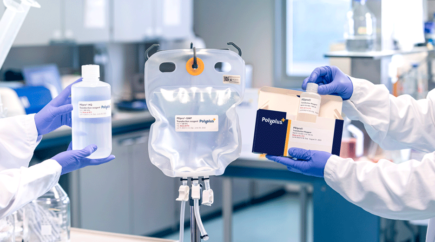
Polyplus and ABL Europe here present data to demonstrate how effective process optimization can be achieved by relying on CDMO expertise and established supplier to achieve scalable USP platform with highest & predictable yield outcomes for a large range of serotypes.
![]() |
Mégane Denu, Bioproduction Engineer at Polyplus®. |
![]() |
Quentin Bazot, Viral Vector Manufacturing and Process Development Specialist, ABL Europe. |
![]() |
Alengo Nyamay’antu, Ph.D, Scientific Marketing & Communication leader at Polyplus®. |
Adeno-associated virus (AAV) has emerged as a leading platform for the delivery of gene therapies due to an excellent safety profile and efficient transduction to various target tissues. Originally focused on ultrarare conditions, the potential to expand applications into more common diseases is vast but requires larger quantities of viral vectors. The shift in demand is driving the need for rapid expansion of commercial AAV manufacturing.
In the last five years, greater numbers of gene therapies have advanced to late clinical stages and commercialization. In 2022 alone, five new approvals were granted in the US and/or Europe.
Yet, at the time of draft, there is no standardized platform approach for commercial-scale AAV manufacturing with predictable yield outcomes such as with monoclonal antibodies (mAbs). This is further complicated by multiple natural serotypes of AAVs, driving hybrid serotypes design to target sites in a patient’s body are being developed. Differences in serotypes can influence the performance of both upstream and downstream AAV production processes, and behave differently during chromatographic separation, making it difficult to create platform purification processes.
For many early-stage companies, or those lacking capital for infrastructure, working with contract development and manufacturing organizations (CDMOs) with experience working with many different viral vectors and genes of interest can be helpful. Their teams can support the development of scalable upstream and downstream AAV production platforms with high and predictable yields for a large range of serotypes.
The early successes of gene therapy have led more companies to pursue the development of additional candidates, driving continued expansion of the pipeline. The number of clinical trials using AAV and LV vectors is growing each year. Currently there are 669 AAV and 266 LV trials in US, 1250 AAV and 94 LV trials in Europe, and 223 AAV and 140 LV trials in Asia-Pacific.1 And as target indications broaden, many candidates in the clinic are conditions that affect much larger patient populations, calling for systemic delivery with much larger doses. All of this continues to increase demand for AAV and LV vector manufacturing.
One of the main challenges with current viral-vector processes is the poor yields they afford—typically 30-40%. Fortunately, there exist opportunities to improve the performance of both upstream and downstream operations. There has been a lot of investigation around improved purification strategies, but there is also a lot that can and should be done in the upstream. Ultimately, improvements in the upstream have a direct impact on the amount of purification required in the downstream.
On the production side, there are a few ways to increase production capacity: add more physical capacity, either by expanding existing sites or adding greenfield facilities; scale existing processing; or intensify processes, which involves improving the efficiency and productivity of manufacturing processes to achieve higher-purity product in less time and in a smaller footprint.
To achieve effective process optimization and ensure ongoing capability to produce large volumes of GMP viral vectors, the quality and security of supply of critical raw materials must be assured. Since there are no strict regulatory guidelines, only recommendations, it is best for manufacturers of viral vectors for gene therapy and other therapeutic applications to use plasmids and transfection reagents from suppliers that have validated processes and offer multiple grades that differ only in the level of documentation (i.e., are of the same quality and purity), allowing for seamless scaleup from the lab to commercial production and avoidance of any regulatory delays. Suppliers of these critical raw material ideally also provide dual sourcing solutions with appropriate supply agreements in place, thus providing security of supply.
AAV vectors can be produced by numerous methods. Regardless of the approach, quality should be built into the process via careful plasmid design, identification/engineering of optimal cell lines, and development of fit-for-purpose media and transfection reagents. Transient transfection involves thawing the cells (HEK293 derivatives for adherent or suspension cell culture), cell expansion, plasmid DNA-transfection reagent complex formation and transfection/AAV production. This is followed by clarification, buffer exchange and concentration via ultrafiltration/diafiltration (UF/FDF), into purification. This is typically chromatographic at scale, because legacy ultracentrifugation processes are lengthy, labor-intensive, expensive, and not readily scalable. Then there is another UF/DF step to establish the final formulation, sterile filtration and fill/finish using equipment designed for the lower titers and different types of vials used with viral vectors.
Across the process, scalability is critical to quality. Ideally there is a representative small scale-down model of the large-scale process to identify relevant critical process parameters (CPPs). Taking this approach allows consideration of not only the impact of serotypes on titers, but full/empty capsid ratios, which directly impact yield and the complexity of downstream purification operations.
Downstream purification must separate the AAV vector product from impurities generated during the manufacturing process while maintaining high infectivity and titer and providing robust and reproducible results. To achieve this, downstream purification processes must be serotype independent.
Optimization of analytics will play a crucial role in the development of an AAV manufacturing platform. Right now, determination of genomic viral titers can often differ from lab to lab, and results of qPCR, dPCR, and ddPCR assays can vary depending on the method specifics. This is not ideal for quality control (QC) or process optimization efforts.
Looking at platform approaches to mAb manufacturing, it is known that using this approach can lead to efficiency and productivity increase.
The challenge for developing an AAV vector manufacturing platform is the use of many different AAV serotypes for the delivery of gene therapies to different organs. Optimum transfection of plasmids to produce different serotypes and AAV vectors for different therapeutic applications can potentially require different cell lines, plasmid construct designs, media, transfection process conditions, harvest methods, analytics, and so on.
Process parameters typically explored include the amount of plasmid DNA, the plasmid:transfection reagent ratio, and the complexation volume and time. These parameters should be considered for each process, as slight changes in their values can result in measurable changes in productivity, titer, infectivity, and so on.
The best approach to optimizing transfection processes for a given AAV serotype and gene of interest is to use a design-of-experiment (DoE) strategy that enables simultaneous evaluation of multiple variables. DoE studies allow visualization of the interactions between factors, which is not possible with conventional one-factor-at-a-time (OFAT) studies.
To identify the optimum transfection reagent for large-scale production of AAV vectors via suspension cell culture, Polyplus completed high-throughput screening of a large chemical library. The work was focused on evaluating chemistries with the greatest potential and performance.
FectoVIR®-AAV transfection reagent—launched in 2020, expanding to GMP grade in 2021—was selected to provide higher titers with simplified protocols, lower complexation volumes, and greater transfection complex stability. It is compatible with different media, cell lines, and AAV serotypes and available in research and GMP grades to achieve more doses per batch for a lower cost/dose.
In validation studies compared to the original gold standard, PEIPro® transfection reagent, FectoVIR®-AAV increases titers by at least two folds with a higher percentage of full capsids (Figure 1).
Figure 1. FectoVIR®-AAV increases rAAV9 titers by at least two folds with a higher percentage of full capsids.
Rather than the typical 10% complexation volumes required to maintain high productivity, volumes of complexation mixtures as low as 1% are effective. For large-scale reactions, this reduction in volume is crucial because there is less time needed for transfer into the bioreactor. Reagent stability also cuts the time required for complexation mixture transfer, even for large-scale transfection processes (Figure 2).
Figure 2 . FectoVIR®-AAV is optimized for large scale reactions with volumes of complexation as low as 1% and stability of complexes for several hours compatible with longer complex transfer time in bioreactor.
CDMO ABL Europe is working on a high-performing transient transfection platform process using HEK293 cells adapted for suspension cell culture at large scale (200L/500L). The platform design is flexible to allow for any modifications needed to maximize serotype production across various scales of early to later-stage projects. The platform is also IP-free to share scientific knowledge for the greater good.
For upstream optimization of the transient transfection process, ABL Europe evaluated the performance of PEIpro® and FectoVIR®-AAV with the Polyplus team. A DoE study was implemented using small-scale (125 mL) shake flasks to identify the CPPs. Further DoE runs were then performed in small-scale bioreactors (Ambr®250 modular system from Sartorius with up to eight vessels), and the process was then scaled to 2-L bioreactors.
Thawing and cell expansion, cell line selection, cell growth, media selection, and passage numbers were optimized. For the transfection step, the ratio of different plasmids, DNA concentration, cell-seeding density, transfection reagent, and transfection reagent: total DNA ratio were evaluated, as well as the feed strategy, lysis conditions, and time of harvest.
For the small-scale DoE studies, a two-plasmid system was employed to produce AAV2, with lysis and clarification performed 72 hours post-transfection. Performance was evaluated based on the vector genome quantity obtained, determined by qPCR.
With FectoVIR®-AAV, the best titers were obtained at a DNA concentration of 0.5µg/ per E6 cells at time of transfection. In addition, the higher the plasmid ratio and cell-seeding density, the higher the titer (Figure 3). On the other hand, the FectoVIR®-AAV:DNA ratio did not have an impact on titer. Processes using the optimum parameters were repeated in the 125-mL shake flasks and run in Ambr®250 mini-bioreactors, resulting in highly reproducible results.
Figure 3 . Small-scale DOE study (125 mL shake flask) showed that with FectoVIR®-AAV, highest AAV2 titers using a two–plasmid system were obtained at a DNA concentration of 0.5µg/ per E6 cells at time of transfection. Further DoE runs were then performed in small-scale bioreactors (Ambr®250, Sartorius), and the process was then scaled to 2-L bioreactors. Performance was evaluated based on the vector genome quantity obtained, determined by qPCR.
Three different media were then used to generatecell banks after adaptation of the cells to the media. Processes were then run using FectoVIR®-AAV and PEIpro®. With FectoVIR®-AAV, there was no difference in the genomic titer, but the particle titer (determined using ELISA) was reduced with two of the media. With PEIpro®, the genomic titer was increased with two of the media. It should be noted that while ELISA and qPCR are not optimal methods for measuring the full/empty capsid ratio, they are still the methods of choice for upstream samples and are proved to be be very useful when comparing samples together.
The process was repeated in a 2 L bioreactor where three independent runs were performed, all provided the expected titer in a highly reproducible manner (data not shown). The transfection process was then repeated using the best transfection parameters identified with FectoVIR®-AAV and PEIpro® to produce different AAV serotypes using the Ambr®250 modular system (smalls scale bioreactor). As expected, higher titers were obtained for AAV2 when using FectoVIR®-AAV, and similar viral titers were observed for AAV8 independently of the transfection reagent used. However, for AAV5, AAV6, And AAV9, higher genomic titers were all obtained when with FectoVIR®-AAV (Figure 4).
Figure 4. Performance using the best transfection parameters for both FectoVIR®-AAV and PEIpro® were assessed for production fo several AAV serotypes, AAV2, AAV5, AAV6, AAV8 and AAV9.
The success of gene therapies and the movement toward treatments for prevalent diseases is creating dramatically higher demand for viral vectors than can be currently met with existing capacity. While expansion can help meet some of this need, it is equally important that the efficiency and productivity of current processes be improved. It benefits the industry to enable more doses to be produced in intensified processes with smaller equipment.
A comprehensive DoE strategy with a platform approach can be powerful. In combination with collaborations like the one between ABL Europe and Polyplus the payout of productivity, safety and efficacy in viral vector manufacturing is as clear as the impact of working with quality raw materials across the process. As processes become further optimized, the industry will see higher generation of functional virus in a smaller footprint with less reagent and media.
Open communication and clear documentation will help streamline the phases of DoE studies from development of transfection processes (deciding, specifying, designing, collecting, analyzing, fitting, and predicting optimized conditions) forward. It is important to understand how the CPPs for different transfection reagents scale.
Finally, testing and assessment of new technologies for AAV manufacturing will help enable even better yields and higher purities via more streamlined and robust processes. If the industry can find ways to maintain or increase quality with less cost of goods (and ultimately, cost per dose), gene therapies have a greater chance of changing life for the better for more patients.
You can also watch our on demand webinar on Building an AAV platform in 2023 : Challenges, Threats and Opportunities.
Reference