Available at research and GMP grade to intensify production of recombinant AAV rAAV viral vectors at any scale from benchtop to 2000L scale bioreactor...
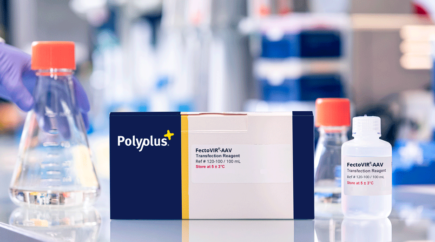
We use cookies to help you navigate efficiently and perform certain functions. You will find detailed information about all cookies under each consent category below.
The cookies that are categorized as "Necessary" are stored on your browser as they are essential for enabling the basic functionalities of the site. ...
Necessary cookies are required to enable the basic features of this site, such as providing secure log-in or adjusting your consent preferences. These cookies do not store any personally identifiable data.
Functional cookies help perform certain functionalities like sharing the content of the website on social media platforms, collecting feedback, and other third-party features.
Analytical cookies are used to understand how visitors interact with the website. These cookies help provide information on metrics such as the number of visitors, bounce rate, traffic source, etc.
Advertisement cookies are used to provide visitors with customized advertisements based on the pages you visited previously and to analyze the effectiveness of the ad campaigns.
Development of an optimal process cannot be achieved without having a deep understanding of the process, including the various factors that can influence yield, quality, and other performance attributes. For transient transfection processes, using a DoE approach leads to optimum processes that maximize cell and system performance by identifying the sweet spot where requirements for excellent cell growth and viability are achieved in combination with high transfection efficiency and generation of a high level of functional vectors
The gene therapy field has exploded in recent years. At the end of 2022, at least 24 gene and gene-modified cell therapies had received marketing authorization worldwide. Five of these were approved in the U.S. that year, the most ever in a single year by the U.S. Food and Drug Administration (FDA).1 Eight more gene and gene-modified cell therapies could receive FDA regulatory decisions in 2023.
Nearly 1,100 clinical trials investigating gene and gene-modified cell therapies were underway in mid-2022.1 Approximately one-third of those trials involved direct gene therapies1, nearly 75% of which rely on recombinant adeno-associated viral (AAV) vectors for delivery of the genetic material.2 Of the 1100 trials, the delivery vector was public information for 45%, with lentivirus predominating (48%), followed by AAV (26%).1 Despite these clinical advances, therapeutic vector manufacturing remains a challenge.
AAV vectors are preferred for the direct delivery of gene therapies because they are not pathogenic and elicit only minimal immunogenic reactions in animals and humans. Targeting a wide range of tissues is also possible with access to numerous wild-type and engineered AAV serotypes, and AAV can deliver genetic material to many different dividing and non-dividing cells. AAV-based gene therapies are consequently in development for a variety of indications, including ophthalmic, neurological, metabolic, hematological, musculoskeletal, and cardiovascular diseases.
The cost to develop, manufacture, and deliver AAV-based gene therapies remains a significant issue, however. Transient transfection processes are often inefficient and unoptimized due to the rush to be first to market with these potentially curative treatments. Typical lab-scale adherent cell-culture processes that involve numerous manual interventions are lengthy, not readily scalable, and generally impractical to implement in a GMP environment. High raw material costs and low yields for viral-vector production are two additional problems that must be resolved.
These factors contribute to a cost of goods for gene therapy manufacturing ranging between $500,000 and $1 million3—which must be reduced if AAV-based gene therapies for the treatment of more prevalent diseases and larger patient populations are to be commercially viable and accessible. As importantly, due to the current process limitations, scaling out and scaling up to the needed volumes is insufficient to meet expected growth in demand at an acceptable cost-per-dose.
Scaling out is accompanied by a linear increase in costs with the use of multiple production trains based on the same inefficient processes and is not a long-term solution. Scaling up to larger bioreactors does reduce operating costs, but again gains are limited by the inherent inefficiency of most AAV manufacturing processes. Process optimization and intensification must be realized in combination with the development of more readily scalable processes.
Due to the complexity of transient transfection processes and the fact that numerous and varied factors can directly impact process performance, one of the most effective methods for establishing optimum solutions is through a design-of-experiment (DoE) approach. Process intensification, meanwhile, can be achieved using fit-for-purpose plasmids and transfection reagents.
Development of an optimal process cannot be achieved without having a deep understanding of the process, including the various factors that can influence yield….